AI in Phosphoric Acid Manufacturing: Enhancing Production Efficiency and Yield
Client Profile
A leading multinational fertilizer company faced significant challenges in their phosphoric acid manufacturing process.
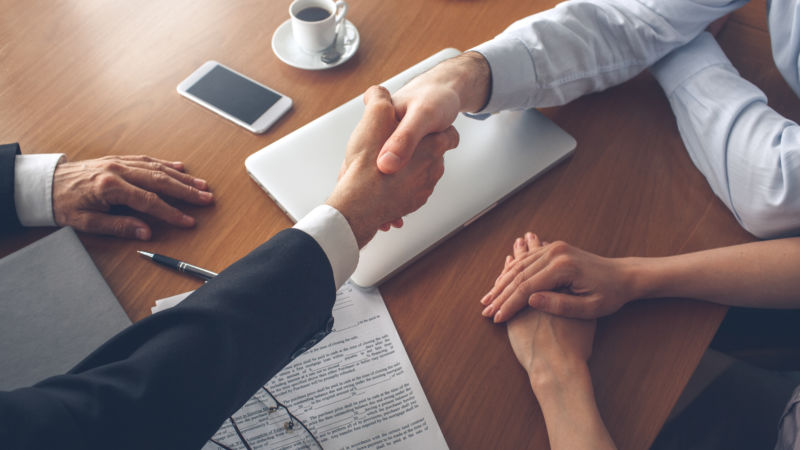
The Challenge
- Facility stuck in upsetting cycle of reactor due to gypsum cluster formation
- Increased filtrate strength creating a cyclic effect as weak acid recirculated to reactor
- Need to optimize the filtration process
- Goal to run at maximum feed rates and reach optimum yield while maximizing operating equipment effectiveness
Process Point's Solution: Data-Driven Intelligence
Data Collection and Analysis
Initial data pull: ~13 million data points
Data cleaning and feature generation: Based on chemical principles and SME feedback
Anomaly detection: Removed anomalous data, resulting in ~2000 features generated
Advanced Modeling and Machine Learning
XGBoost: Utilized for identifying important attributes
K-Means clustering: Chosen to identify various operating modes
Support Vector Machines (SVMs): Used to smooth out clusters and find optimal operating points
Real-Time Monitoring and Optimization
Soft sensor development: Informs operators how close the system is to the inflection point of feed vs filtrate based on current conditions
Set point and cluster confidence metrics: Developed for real-time monitoring
Recommendations: Provided to operators when cluster confidence is above set threshold
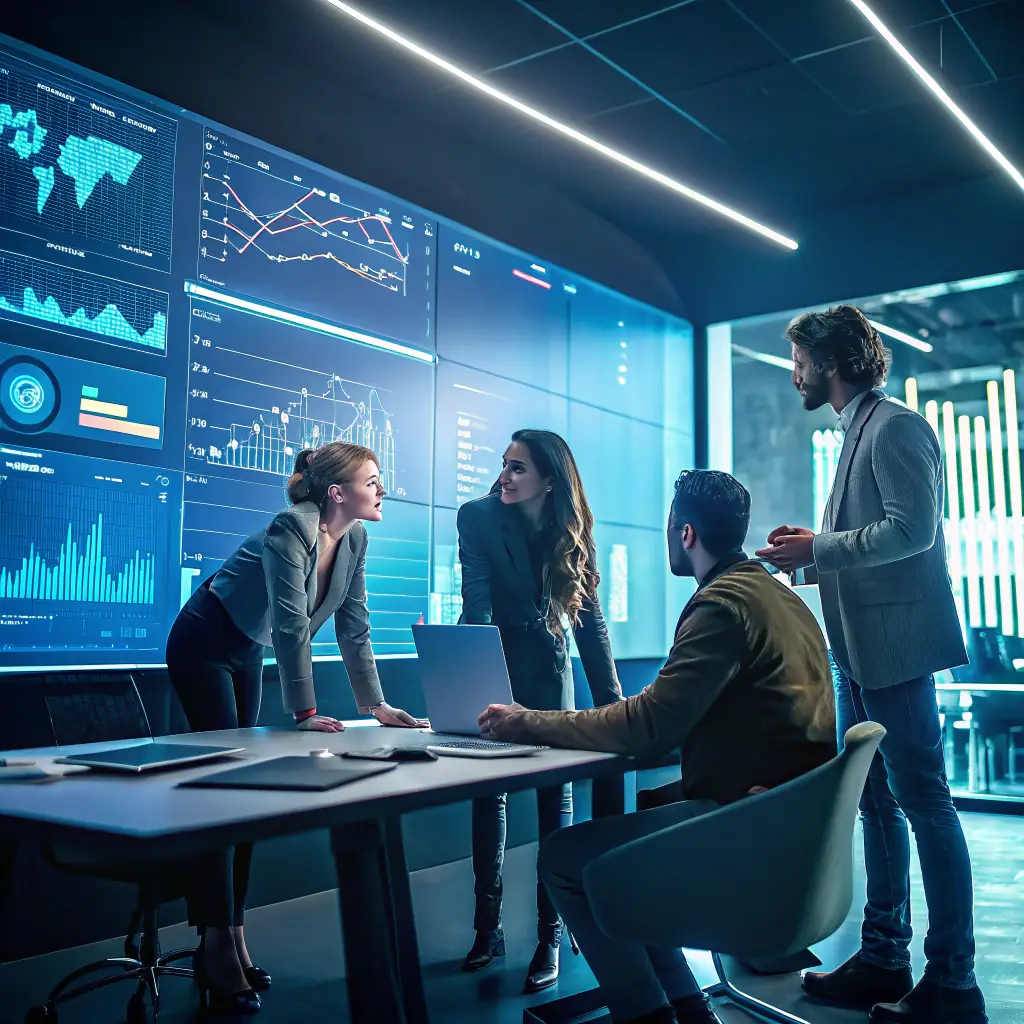
Our Proven Results
Conclusion
- Expertise Utilized: Process Point’s data-driven approach.
- Optimization Achieved: Successfully optimized the client’s phosphoric acid manufacturing process.
- Challenges Addressed:
- Gypsum cluster formation
- Cyclic effects impacting efficiency
- Technologies Used: Advanced analytics for industrial problem-solving.
- Results:
- Improved efficiency in manufacturing.
- Increased yield of phosphoric acid.
- Enhanced equipment effectiveness and longevity.
- Industry Impact:
- Demonstrates the power of data-driven strategies in industrial transformation.
- Sets a new standard for industrial optimization in the Industry 4.0 era.